

Vacuum: The framework containing the heated, pliable sheet of plastic is lowered over a mold and pulled into place via a vacuum on the other side of the mold. Heat: The plastic sheet is softened using a heat source until it reaches the appropriate forming temperature and becomes pliable. The step-by-step vacuum forming process works as follows:Ĭlamp: A sheet of plastic is placed in an open frame and clamped into place. With female molds, the thermoplastic sheet is placed inside the mold to form the outer dimensions of the part precisely. With male molds, the sheet of plastic is placed over the mold to contour the inside dimensions of the plastic part. There are two basic types of molds-male or positive (which are convex) and female or negative, which are concave. It is ideal for parts that only need to be precisely formed on one side, such as contoured packaging for food or electronics.
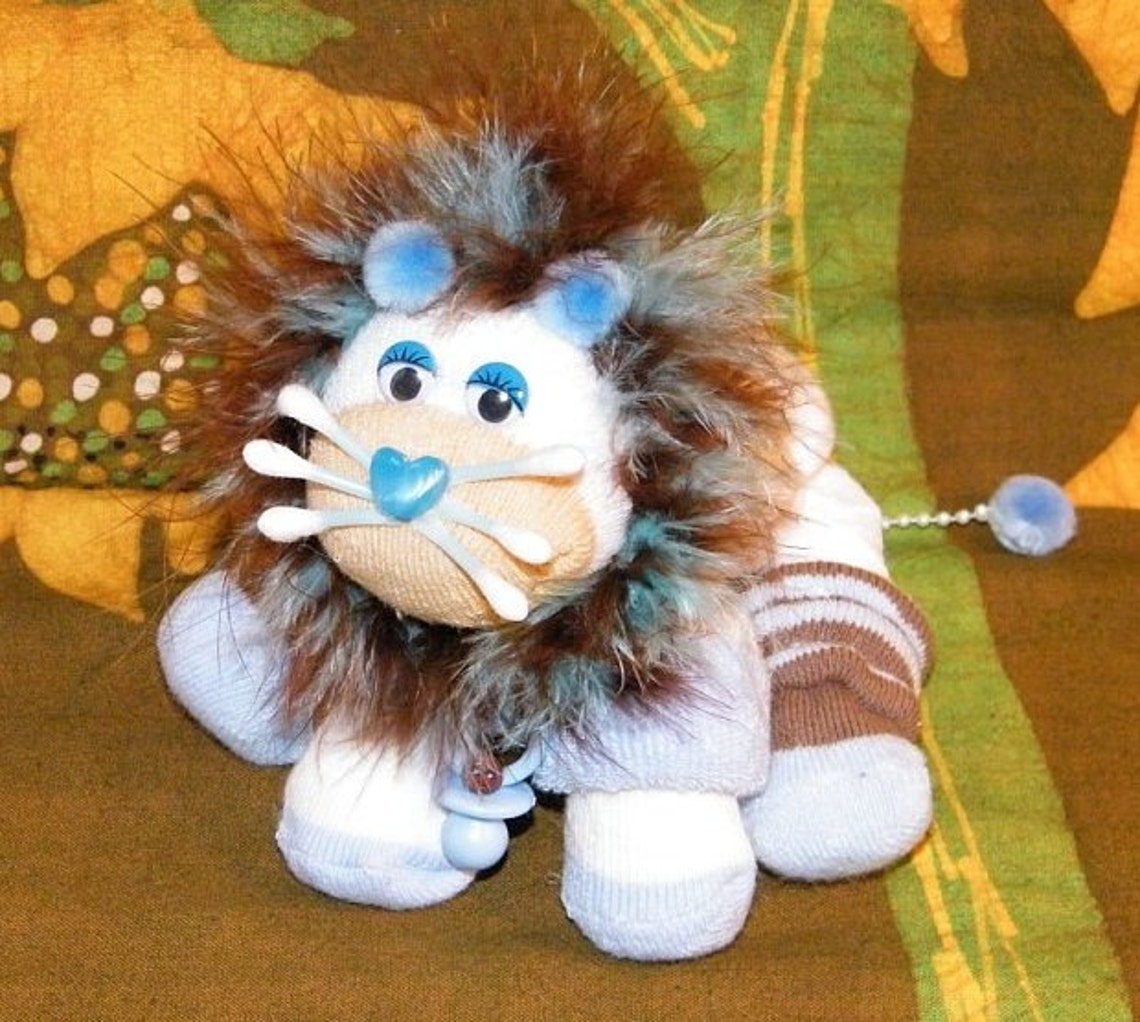
Vacuum forming is the simplest type of plastic thermoforming, that uses one mold and vacuum pressure to obtain the desired part geometry. The main difference between pressure forming and vacuum forming is the number of molds that are used. Vacuum forming and pressure forming are both different types of thermoforming processes. Thermoforming is a manufacturing process where a sheet of plastic is heated to become pliable, then shaped or contoured using a mold, and trimmed to create a final part or product. What are the Differences Between Vacuum Forming, Thermoforming, and Pressure Forming? Vacuum forming is used for a wide range of manufacturing applications, ranging from small custom parts produced on desktop devices to large parts manufactured on automated industrial machinery.
